UV Lithography :
Ebeam Lithography :
Nettoyage des substrats :
Wet chemistry
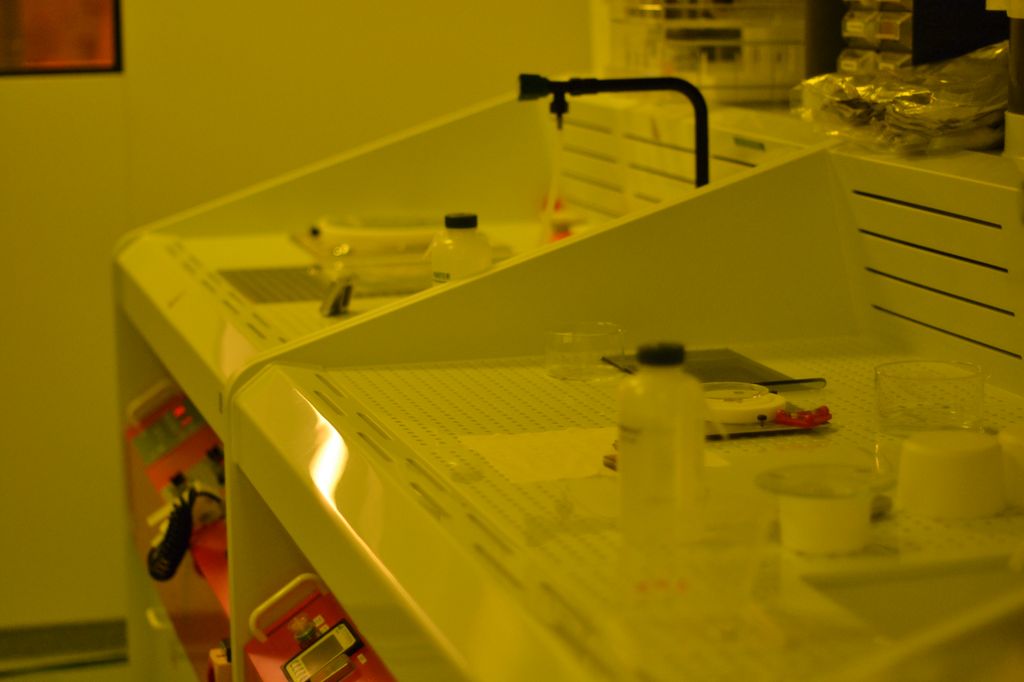
Piranha
When classical solvents are not enough strong to remove organic residues, “piranha” solution which is a mixture of sulfuric acid (H2SO4) and hydrogen peroxide (H2O2). This mixture is also really efficient for mask cleaning (to remove resist residues after lithography)
Solvents
The standard process to clean organic residues off substrates is:
These operations should be done only under the solvent fume hood (stainless steel).
- Acetone (5-10 minutes, sonification if possible)
- Ethanol or Isopropyl alcohol (5-10 minutes)
- Nitrogen gun drying
Plasma Cleaning
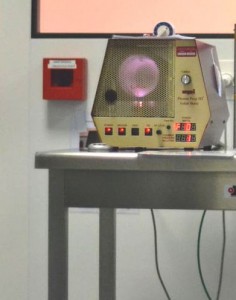
- power : 100 W
- gas : pure oxygen (99.999%)
- frequency : 13.56 MHz
- working pressure: 200 mTorr
- 100 mm Pyrex chamber
Oxygen Plasma
Oxygen plasma cleans off organic residues without using solvents. Key features of Plasma Prep III :
UV/ozone
UV/ozone cleaner cleans off surfaces slightly contaminated with organic residues. This equipment can also be used to activate surfaces for a better adhesion of resist.

Materials :
I. Chemicals
Acids and bases
Product | Composition | Ratio in volume |
---|---|---|
Hydrofluoric Acid concentrated 40% | HF 40% | |
Sulfuric Acid | H2SO4 96% | |
Buffered Hydrofluoric Acid, BOE 7:1 VLSI | NH4F 40% + HF 50% | 7:1 |
Buffered Hydrofluoric Acid, BOE 25:1 VLSI | NH4F 40% + HF 50% | 25:1 |
Phosphoric Acid 85% VLSI | H3PO4 85% | |
Cyclohexanone 99.8% VLSI | C6H10O | |
Chlorhydric Acid 37% | HCl 37% | |
Nitric Acid (65%) | HNO3 65% | |
Acetic Acid (99.8%) | C2H4O2 | |
Potassium Hydroxyde pellets | KOH 40% | |
Chromium etch 651826 Aldrich | (NH4)2 Ce(NO3)6; HClO 4 | |
Copper etch Type CE-100 | ||
Au etch | KI (40g.), I2 (1g.), H2 O (80 ml) | |
Hydrogen peroxide 30% | H2O2 30% | |
Ammonium Fluorid 98% | NH4 | 45gr/100 ml H2O |
Ammoniaque 28% | NH4OH 28% |
Resists and developers
Product | Remarks |
---|---|
AZ 1505 | photosensitive positive, 0.4 – 1.0 µm |
AZ 5214 | photosensitive réversible, 0.7 – 1.5 µm |
AR-P 669.04 et AR-P 679.02 | e-beam positive |
SX AR-PC 5000/90 | conductive protective coating for e-beam resists |
MCC SU8-2050 | negative tone epoxy |
MCC SU8-2100 | negative tone epoxy |
LOR 3A | non photosensitive |
Developer MIF 726 | developer for AZ52xx, S18xx |
Developer AZ | developer for AZxxxx |
PGMEA | developer for SU8 (1-Methoxy-2-Propanol Acetat) |
Developer AR 600-56 | developer for AR-P xxx series |
HMDS Microposit primer | Primer |
PDMS Sylgard 184 Silicone elastomer | Base + curing agent/td> |
Solvents
Product | Composition |
---|---|
Ethanol | C2H5O |
Isopropanol | C3H8O |
Aceton | C3H6O |
Remover 1165 | PGMEA, NMP 93% |
AZ100 Remover | remover for AZxxxx |
Remover PG | remover of PMGI, PMMA, SU-8 |
Technistrip NI555 | remover for Novolak-based negative resists |
Remover AR 600-71 | remover for AR-P xxx series |
Stopper AR 600-60 | stop development process for AR-P xxx series |
Extran MA02 neutral | Glass cleaning agent |
II. Wafers
Silicon Wafers
Name | Diameter [mm] | Thickness [µm] | Orientation | Conductivity type, Dopant | Resistivity range [ohm.cm] |
---|---|---|---|---|---|
Silicon prime wafers, 3″ | 75.3 | 350 ± 25 | 100 | P, Boron | 1-3 |
SiO2 Wafers
Name | Diameter [mm] | Si wafer Thickness [µm] | oxide Thickness [nm] | Orientation | Conductivity type, Dopant |
---|---|---|---|---|---|
SiO2 wafers 3″ | 75.3 | 350 ± 25 | 500 | 100 | P, Boron |
III. Masks
Name | Specifications |
---|---|
Chrome Blank 5″ | résolution standard : 4 µm |
Masque souple 2 – 4″ | résolution minimale : 10µm |